Case Design
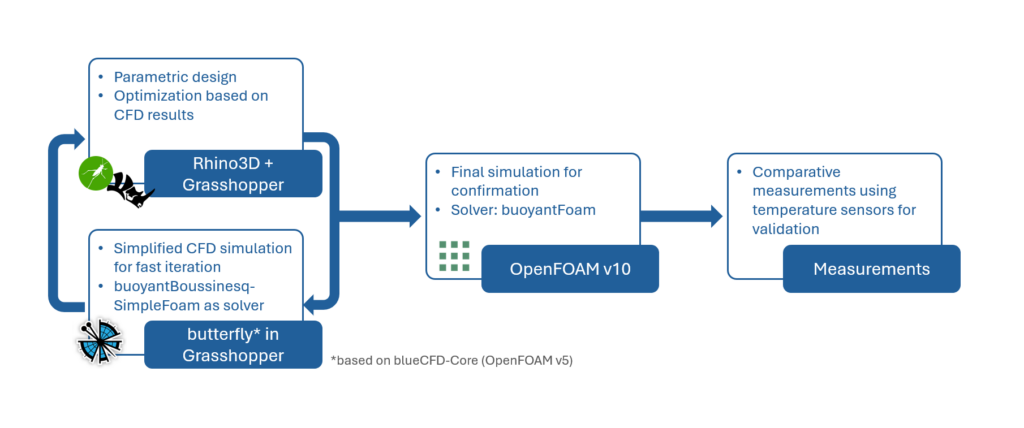
The case of the resource guardian was designed using parametric design in combination with CFD simulations. The design phase included the following step
- First parametric design of the case in Rhino3D and Grasshopper.
- A simplified CFD simulation using the Butterfly plugin in Grasshopper to evaluate the effects of the microcontroller chip’s waste heat and the touchscreen on the sensor.
- Based on the simulation results, the parameters are adjusted to optimize the case design.
- After iteration, the final version is simulated again in OpenFOAM v10 with more detailed settings to ensure simulation accuracy.
- After 3D printing the case, temperature sensors were used to validate how the waste heat affects the sensors.
The goal of the workflow described above is to minimize the effects of the heat generated by the microcontroller and touch display (see thermal camera photo below) on the accuracy of the temperature measurement.
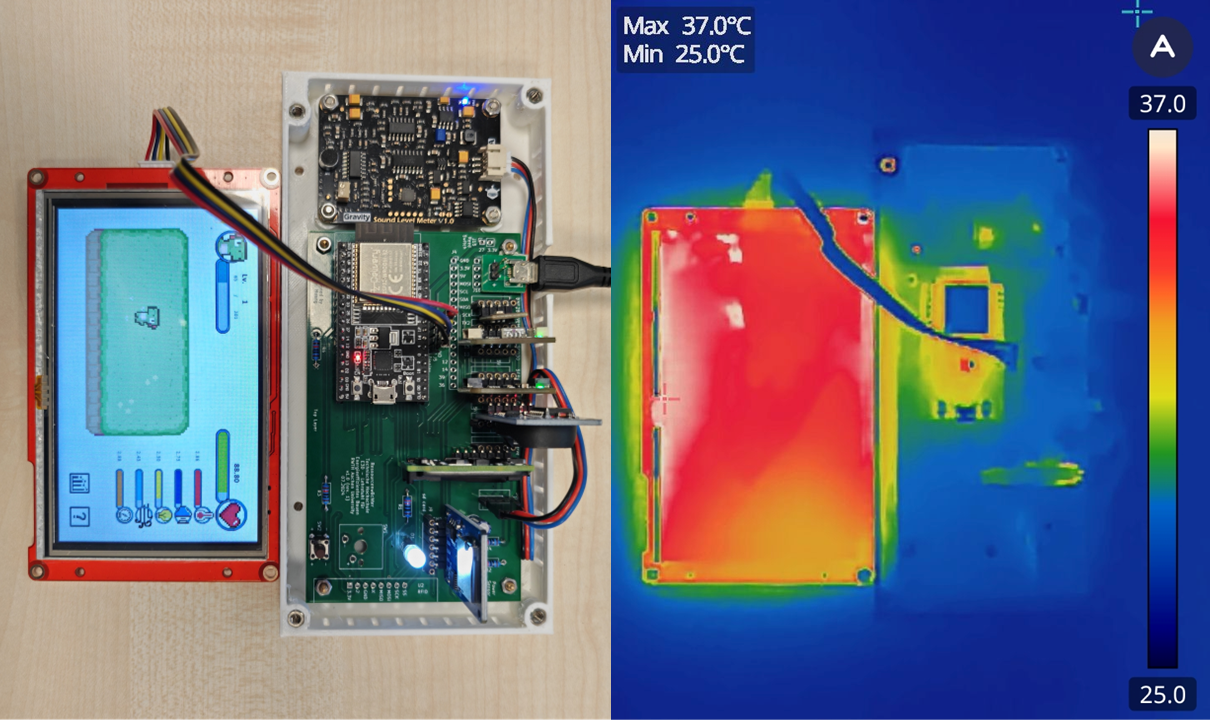
After optimization, the sensors and microcontroller are housed in two separate chambers to control the effects of waste heat to within 0.5 K. The air vents are also optimized accordingly.
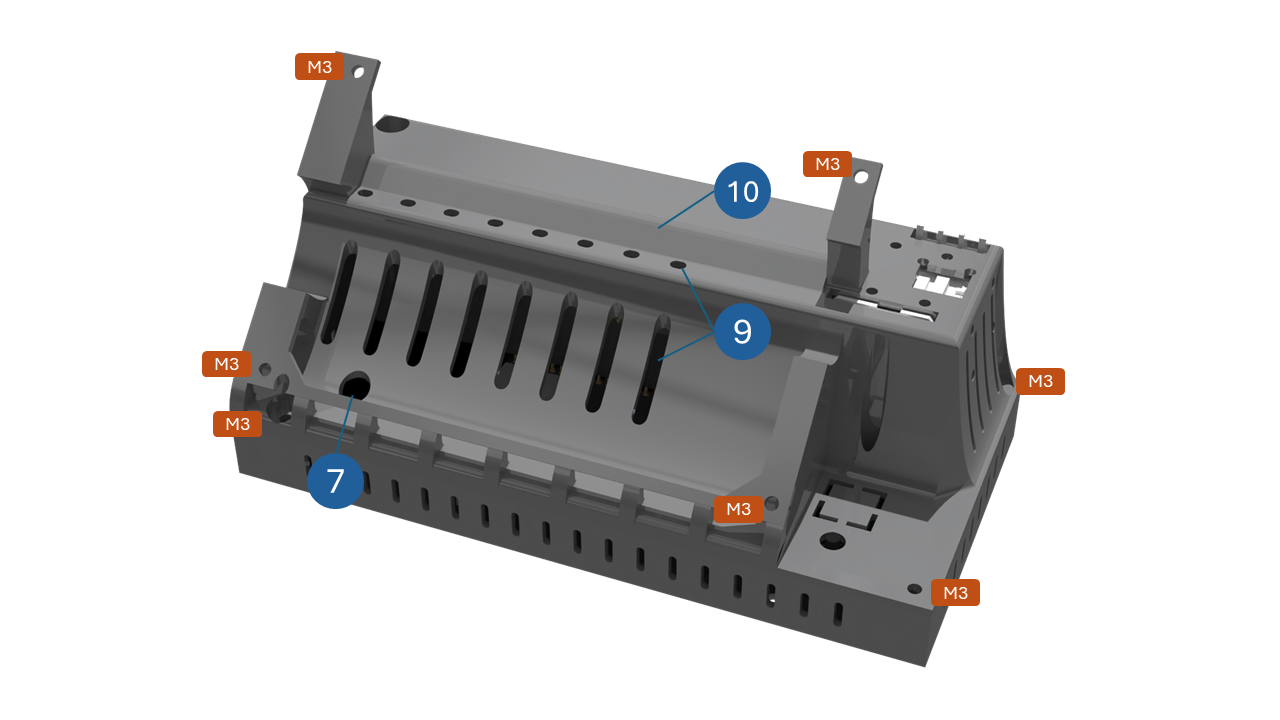
- (7) Opening for the sound level sensor
- (9) Ventilation openings
- (10) An “empennage” that reduces the impact of waste heat in unfavorable wind directions.

(2) Buttons
(3) LED indicator
(11) RFID (optional)
(12) RTC
(13) SD card module
(14) Microcontroller (ESP32)
(15) Window contact (reed switch)
(16) Power Supply
(17) Sensors
(18) Power sensor
(19) Sound Level Sensor
(20) Display Connectors
(21) Reserved Connectors
(22) Partition between MC chamber (A) and sensor chamber (B)
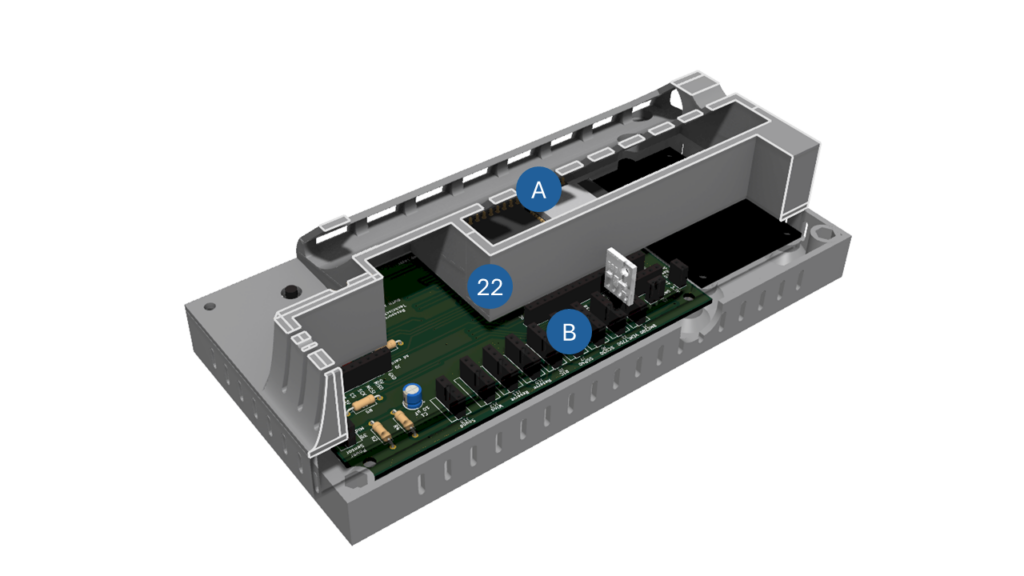